Engeman operates in four major areas:
- Manufacturing of water tube boilers, flame tube boilers, and biomass-fired mixed boilers;
- Heat exchangers;
- Manufacturing of driers for cob corn with temperature control;
- Energy production designs for Thermal Power Plants (UTEs).
A vast know how acquired in the areas of biomass burning and the manufacture of radiators for air heating, supported by a close relationship with the Brazilian agribusiness industry, have placed Engeman as a leader in the manufacture of boilers for drying grains and seeds in Brazil.
Our pioneering and excellence spirit, together with major partnerships, have taken us to new markets in over ten countries throughout Latin America, Africa and Southeast Asia.
INSIDE-THE-FENCE ENERGY GENERATION
- Working full capacity during peak hours;
- Energy compensation during other times;
- Generation of energy credits for consumption within 5 years;
- Shared generation with other companies;
- Commercialization of the surplus;
- Increase of energy efficiency in the biomass consumption;
- Profitable disposition of the surplus biomass;
- Savings in shipment of the surplus biomass;
- Power independence for the utility company;
- Lower production costs thanks to lower power bills.

GENERATION AND COGENERATION
Generation of Biomass is a clean and cost-saving option. ENGEMAN’s thermal and electric energy generation portfolio includes a line of equipment that matches the size ranges required by distributed power systems. ENGEMAN systems have the capacity to burn several kinds of fuels to allow for greater flexibility and use of potential fuel sources available in each case.
COGENERATION
Generation depends on the process steam output, with greater specific steam consumption and lower cost for each generated MWh.
PURE GENERATION
The Pure generation process is independent, but the cost per MWh is greater than in cogeneration.
INVESTMENTS AND EFFICIENCY
Most benefits from Cogeneration plants (CHP) come from a decisive advantage: their efficiency.
While only a small part – 35%-60% – of the fuel used in conventional plants is converted into energy, Cogeneration plant energy efficiency can reach up to 90%, thanks to the use of heat.
For your businesses, this means lower production costs for the same amount of energy generated.
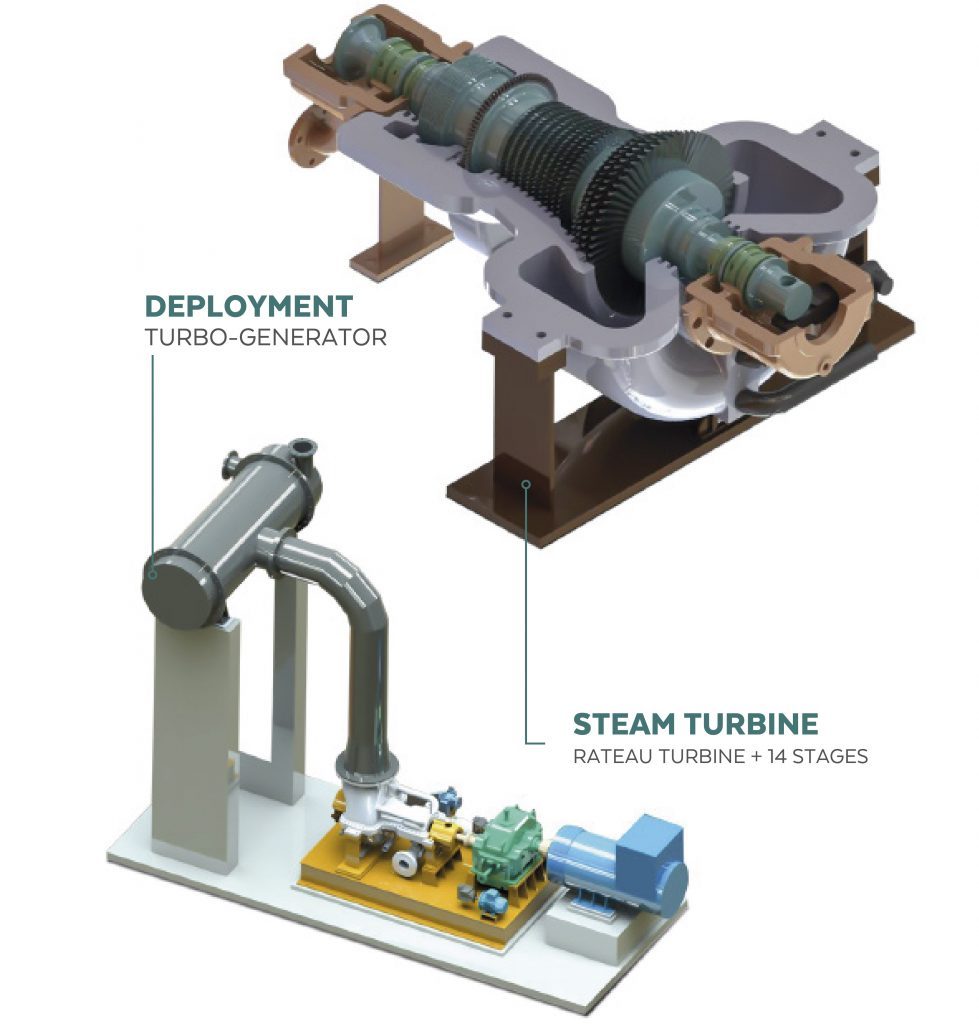
COGENERATION
WHAT IS COGENERATION?
It is the simultaneous production of at least two forms of energy: electricity and heat.
HOW DOES IT WORK?
Generation of at least two forms of energy: electricity and heat. Back pressure turbine.
The steam is produced in the boiler under high pressure and is first directed to the turbine-generator set, where the electricity is generated.
After going through the turbine, the steam is vented at a lower pressure.
This steam can be used for plant processes requiring heat, like drying of grains, dairy products, cooling using adsorption chillers, preparation of foods, etc.
GENERATING ENERGY TO USE AND TO SELL
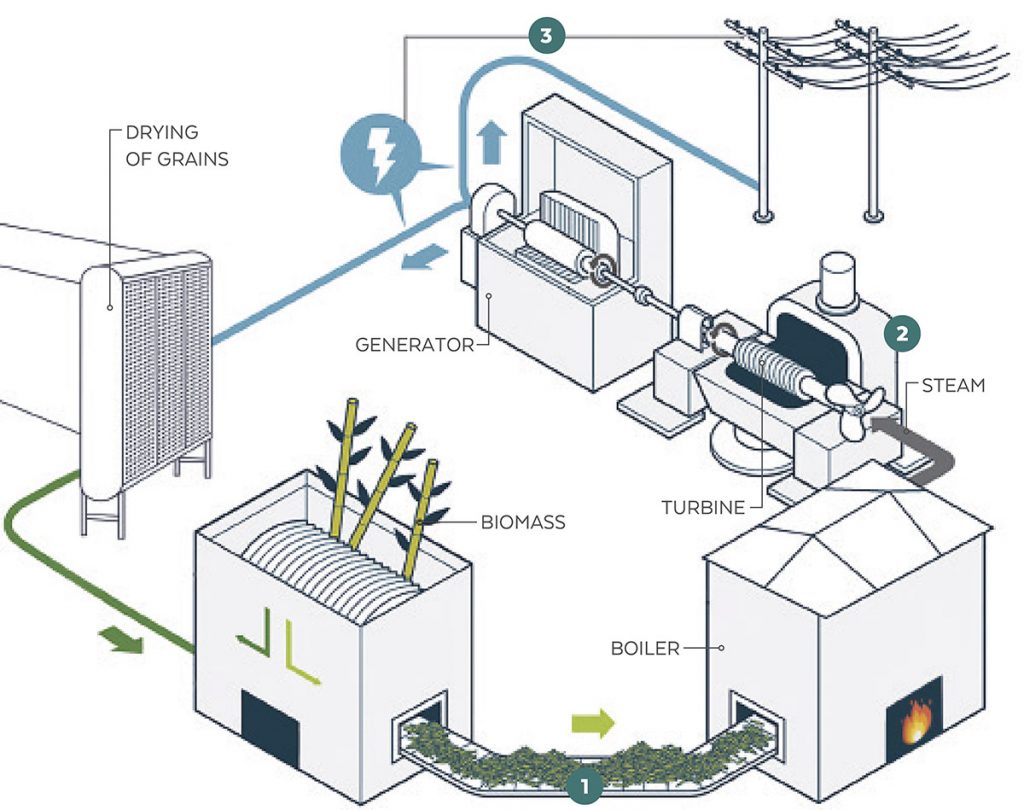
- The Biomass is processed and goes on to the boiler..
- The water steam is produced in the boiler by means of a turbine and a connected generator converts mechanical into electric energy.
- Some of the energy is used by the plant itself, and the surplus can be sold. After going through the turbine, the steam can be used to heat several processes.
WHAT IS PURE GENERATION?
It is when a plant is assembled solely to generate electric energy.
COGENERATION
- Generation of at least two forms of energy: electricity and heat.
- Back pressure turbine; a controlled-extraction turbine can optionally be employed.
GENERATION
- Exclusive generation of electricity.
- Vacuum condensing turbine.
SIG – UTE PROJECT
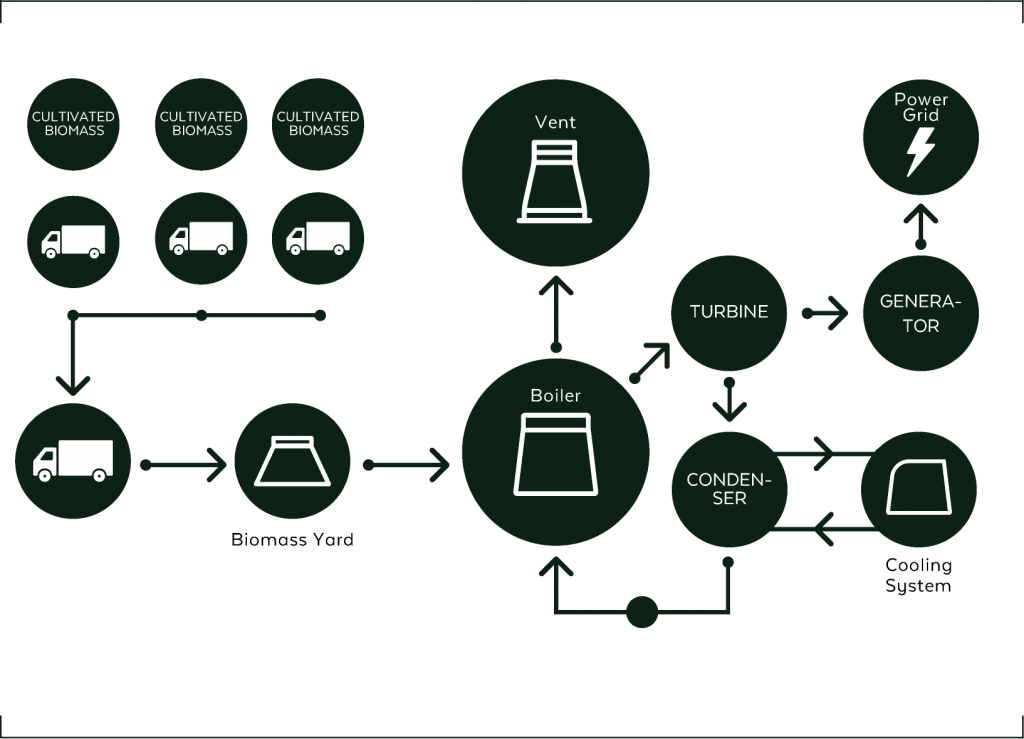
WORK STAGES
1. FEASIBILITY ANALYSIS
- Available resources
- Available fuels
- Place for deployment
- Power consumption
2. SOLUTION DESIGN
- Understanding of the customer’s requirements
- Selection of technology and equipment
- Conceptual design
3. DEPLOYMENT
- Turn Key Regime
- Equipment manufacture
- Assembly of equipment/Electrics
- Project management
- Commissioning and Start-up
4. OPERATION AND MAINTENANCE
- Local trained team
- Training of operators
- Performance Maintenance