Engeman boilers have reached a new quality, efficiency and safety level. Engeman boilers are built according to the ASME standard using high-level raw materials and with strict quality. They can produce from 4 to 40 TPH of saturated steam at pressures of up to 21 kgf/cm2, for several different applications.
Engebio boilers can be set up to burn woodchips, sawdust, and other kinds of biomass like coffee husks, rice hulls, corncobs, etc.
The VULCANO boiler is a new lower cost design that provides greater savings. It is more compact and changed the boiler market by producing up to 8 TPH with stationary or moving grates.
TITAN and THOR boilers are ideal for burning biomass with moisture contents even greater than 45%. They are larger and more robust boilers, and their design includes greater automation and control. Each design is customized, and our company offers a range of fixtures designed to meet the specific requirements of each customer.
Characteristics
- Mixed boiler to burn biomass with a moving grid
- Production of saturated vapor
- Capacity for 4 to 40 TPH
- Pressure of up to 21 kgf/cm²
Advantages
- Heat efficiency between 82 and 88%
- Low fuel consumption
- Lower set up cost
- Easy to operate and maintain
- Uses a variety of fuels
- Production automation
- Low emission of pollutants
THOR BOILER
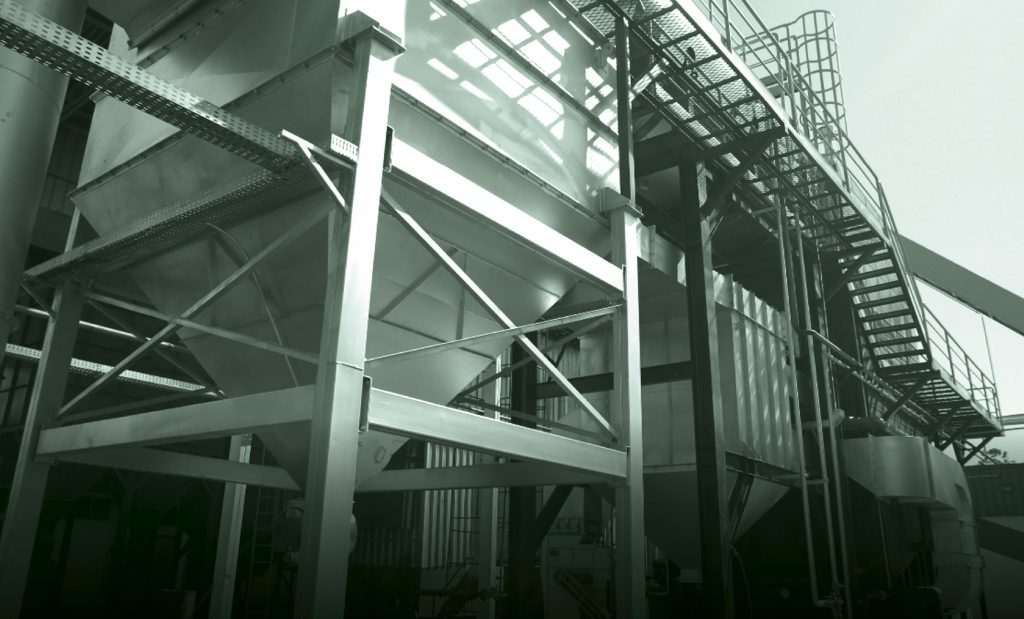
* Woodchips with 1780 kcal/kg heating value and 50% humidity.
TITAN BOILER
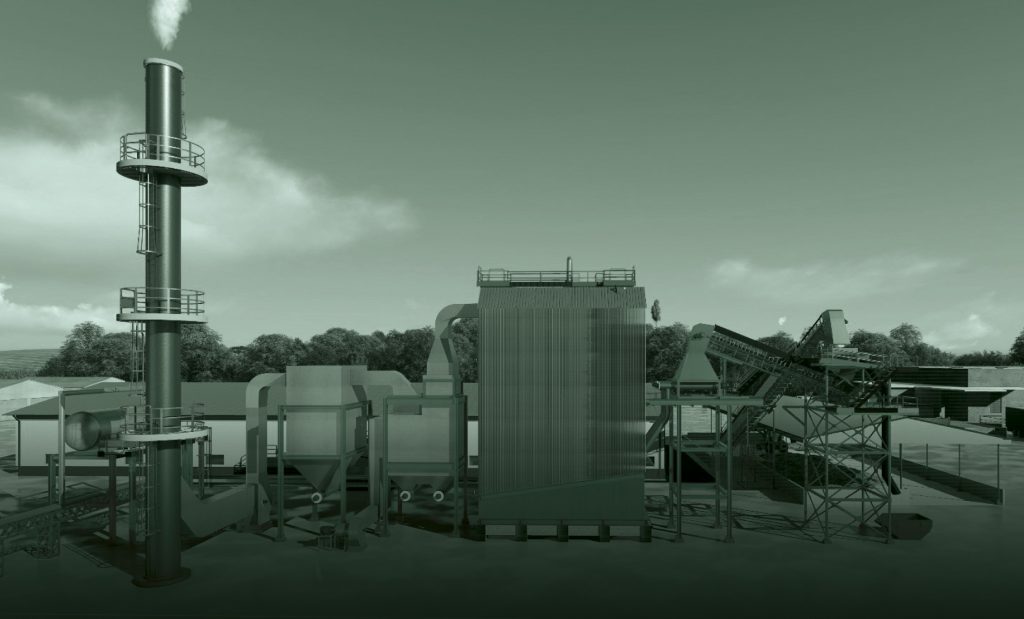
HEAT EXCHANGERS
With applications in several industrial and drying processes, they are a vital component for a clean, fast and safe drying process.
With a high level of precision, they are used, for instance, to dry coffee, soybean, corn, haricots, cotton, cocoa, Brazil nuts, rice, etc.
Their main characteristics are:
- Used in heating air to dry grains and seeds in general;
- Customized designs based on the application, the process involved, and its energy requirements (kcal/Kg);
- Manufactured using DIN 2458 carbon-steel pipes;
- Semi-corrugated helical blades made of SAE 1008 steel.
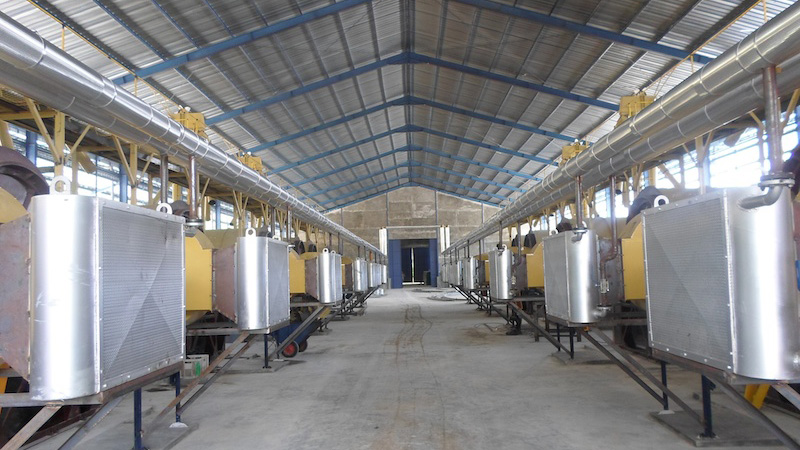
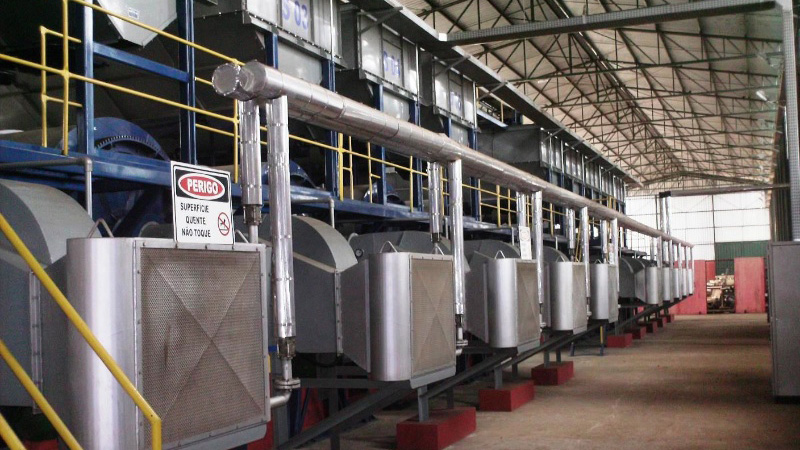
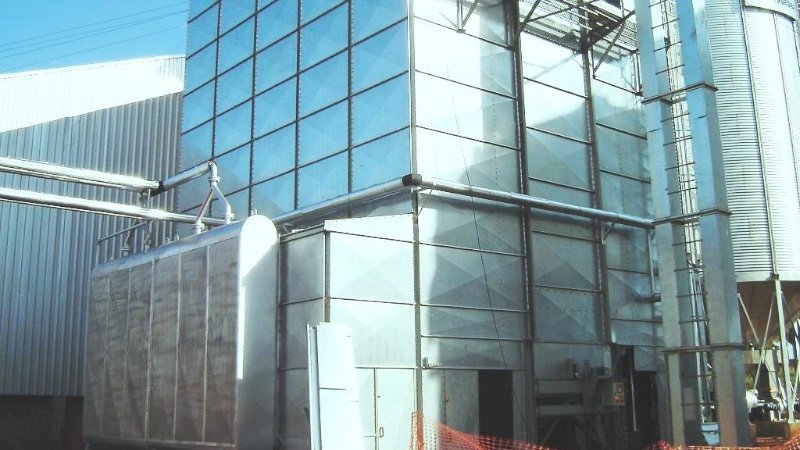
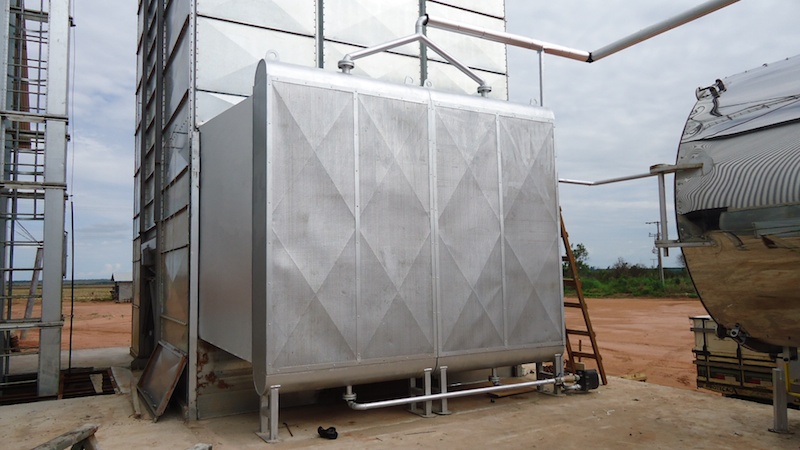
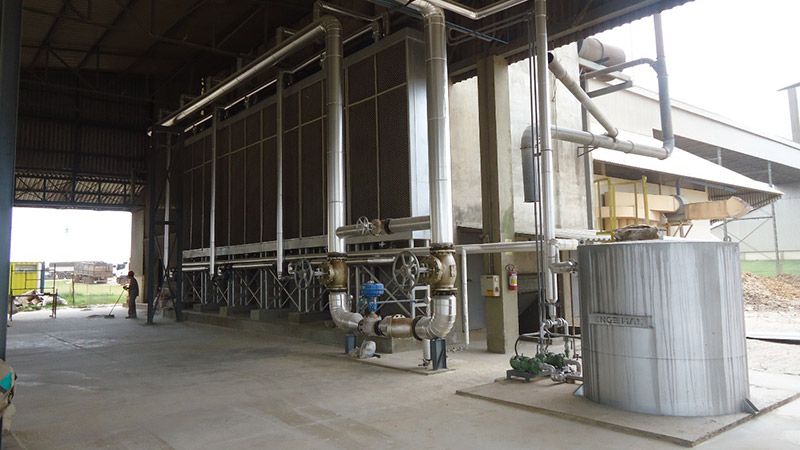
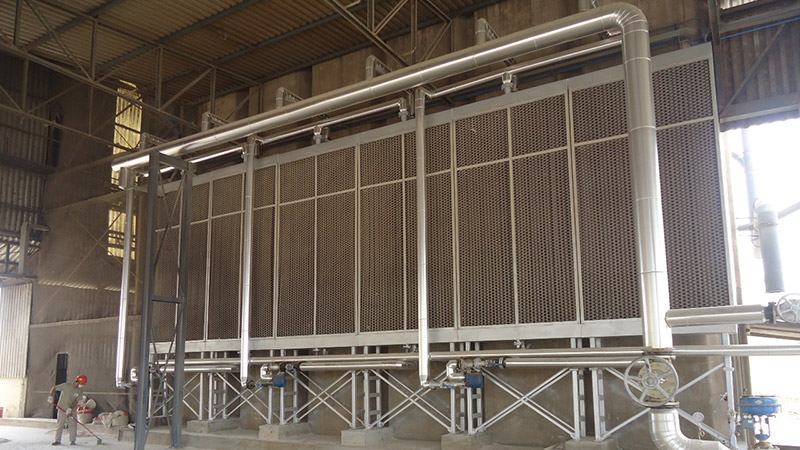
FIXTURES
Meeting environmental and fire safety legislation is something Engeman is always concerned with. That is why we have developed the Multicyclone to meet CONAMA Resolution 382/2006. Other standards can also be met, depending on the project.
Filters of the multicyclone type are the solution for equipment operated in farming regions and in the vicinity of urban regions, as they decrease release of particulate material into the environment and retain sparks within the vent.
Used to increase the boiler thermal efficiency, it works based on an exchanger to heat the primary air (which is required for burning the biomass) by using the combustion gases.
A good temperature control for grain driers brings advantages like a homogenous drying both during the day and at night, a decrease in fuel consumption and issuance of managerial reports for the batch drying process.
It consists in placing vapor flow control valves in the vapor grid and automated temperature sensors and controllers in the drier.
A Redler-type extraction system for the moving grid and a continuous ash extraction system made up of conveyor belts or helical threads, with rotary valves for the multicyclone and an air preheater.
Automatic dispenser silos are employed for dosing the biomass in the boilers; these include helical threads with frequency inverters and a level sensor.
This equipment allows for automatic dosing of the biomass according to the working pressure, vapor production and the speed setting for the boiler feed grills.
We have a woodchip yard for storing and conveying woodchips that includes a steel warehouse, motovibrators, threaded feed hoppers, belt conveyors, and disc sorters.
The seamless working of the Woodchip Yard allows for the full automation of the use of biomass in biomass-fired boilers.
This equipment allows for automatic dosing of the biomass according to the working pressure, vapor production and the speed setting for the boiler feed grills.
Always having safety, quality and savings in mind, we have developed the required automation for the vapor production process. The automation includes fuel and water intake, vapor production control, and failsafes.
A good automation system allows controlling of vapor production, heat efficiency, working pressure, vapor cost, etc. during all production shifts. This way, it is possible to assess whether biomass-fired boilers are operating well, as well as produce monthly reports for management control.